Stainless steel processing cell gets final piece of the jigsaw at KMF
1 min read
KMF (Precision Sheet Metal) has invested further in its manufacturing capabilities, with the completion of a new stainless steel processing cell that went into full production with the installation of a Kuhlmeyer ZBS belt grinding machine, from Ellesco.
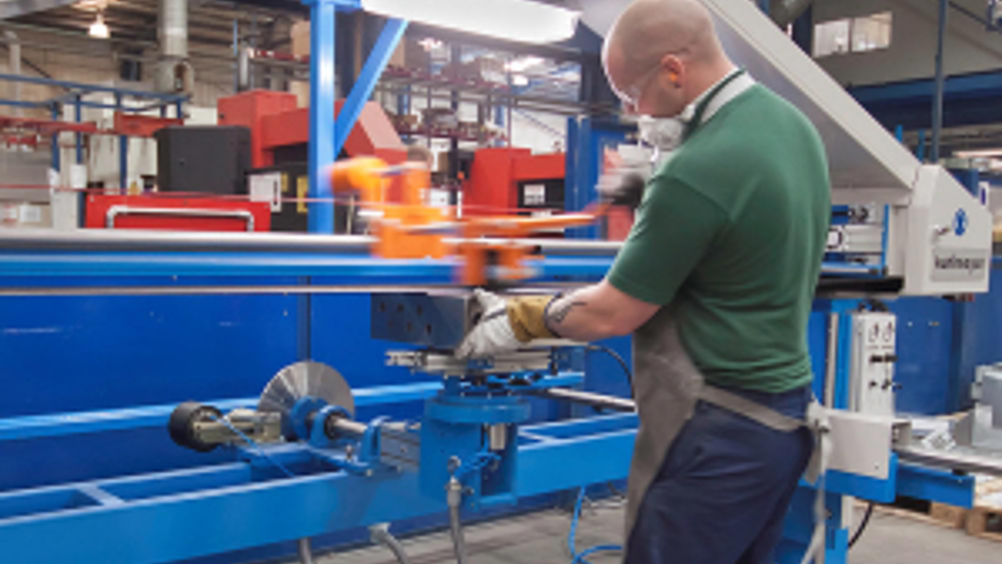
The cell, which includes folding, spotwelding and CNC studwelding, was set up to speed up the processing of stainless steel sheet metal assemblies, and to increase the overall capacity of KMF's manufacturing facility in Newcastle under Lyme.
"The cell will give us a focused approach to resolving the issues normally associated with this type of manufacturing processes," explains Keith Nicholl, business mprovement manager, KMF. The Kuhlmeyer machine is the final piece in the jigsaw and part-automates the linishing and deburring of the stainless steel fabrications.
The portal design of the Kuhlmeyer ZBS machine enables fabrications of up to 3 m in length to be processed, while the continuous belts allow roughing and finishing in the same setup, making it a highly productive and efficient machine. In addition, the open operating environment makes loading and unloading straightforward and once loaded, components can be easily positioned using the machine's workpiece handling system, which uses vacuum clamping to enable multiple faces of a component to be processed in a single set-up, and significantly reduces the manual lifting/manouvering of components, greatly reducing operator fatigue. The operator then simply applies pressure using shaped hand-tools or the machine's pressure pad to complete the finishing operation.
"This element of automation and ease of operation was an important factor in the purchase of the Kuhlmeyer machine," says Gareth Higgins, managing director, KMF. "Throughout the factory, we use automated processes to generate greater manufacturing efficiencies through faster and more consistent processes. But it also plays a vital role in maintaining the health and safety of our staff by reducing the requirement to lift and manipulate heavy and awkwardly shaped components."