Intelligent injection moulding from the EMold Project
1 min read
An event was held recently to mark the successful completion of the collaborative European EMold Project.
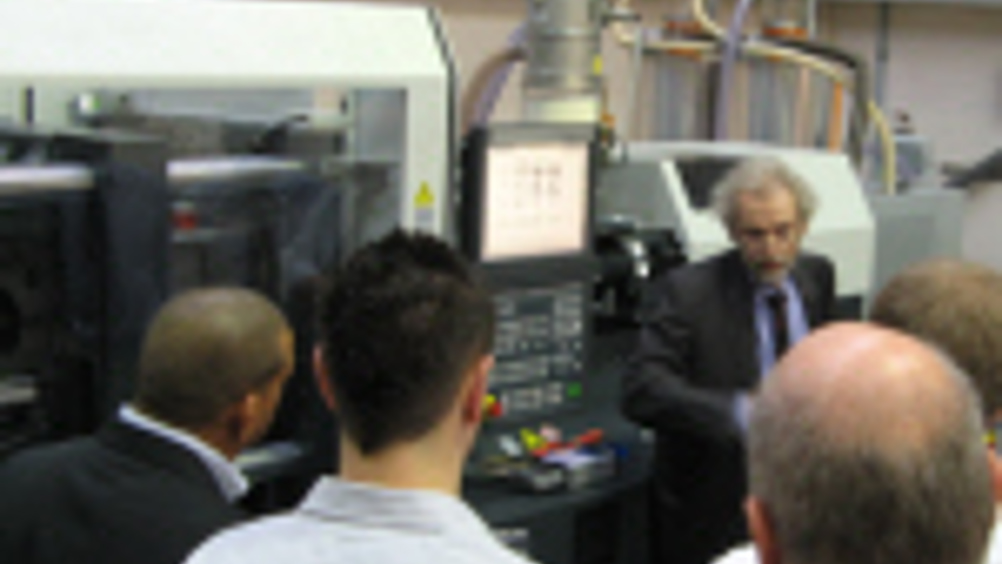
The goal of the EMold Project, in which 17 European organisations participated, was to turn plastic injection moulds from passive elements into active production tools, endowed with embedded knowledge. This would enable the efficiency of plastic part production to be greatly improved, through being able to monitor and correct process parameters.
One of the EMold Project partners, FOS Messtechnik, has developed a sensor which combines a cavity pressure sensor, a mould surface temperature sensor and an infrared melt temperature sensor. This combination of sensors enables the most important physical parameters of the injection moulding process to be measured together in real time.
The E-box represents the brains of the mould, providing communication between the mould and the outside world. It has the facilities for setting up and calibrating, the pressure and temperature sensors, and also:
• Provides basic processing of the signals from the sensors (amplification, noise reduction, etc.)
• Connection with electronic markers, mounted in the mould, with the ability to read their signals
• Connection with an injection moulding machine to read the machine parameters
• Standard wireless TCP/IP protocol network connectivity
• Data encryption
• Closed-loop process control
A case study was discussed, involving the correction of splay marking defects in polycarbonate lenses used in a maritime application, by changing injection moulding parameters with the aid of EMold sensor measurements.
One of the members of the EMold consortium, Eleda Cumsa (Spain), has expressed interest in manufacturing and marketing the E-box.
The event was hosted by the GTMA which represents leading companies in the tool making, metrology, precision machining, rapid product development and tooling technologies. The GTMA is a focal point for technology transfer, as well as providing legal and business support to its members.
Image: John Hind demonstrating the E-box to participants at the EMold seminar held at Sumitomo SHI Demag, while it was in operation on one of their injection moulding machines.