"One hundred and thirty-odd SMEs exhibit here instead of going overseas," says Sir Gerald Howarth who is the president of the British Air Display Association and a firm believer that aerospace is still the UK's biggest area of expertise in manufacturing. While Sir Howarth, being a pilot, talked up the flying aspect of the show, he was equally excited about the business opportunities. Farnborough takes place every other year, alternating with the Paris Air Show, and is the place to talk aerospace business. Over $87 million of sales were completed during the show's now-famous Monday to Thursday trade week in 2012, which in turn has dictated the rhythm of aerospace production since then. This is exactly why Machinery attended the media day in May, and why we have also asked a selection of production companies in the UK to tell us what they plan to show at the event and why.
While Farnborough is number one for business, the organisers aren't complacent. The Berlin airshow is held just a few months before "no coincidence", says, FIA CEO Shaun Ormrod, hinting that Berlin is trying to claim the number one spot. To defend its position, Farnborough is putting on extra events and activities this year to help companies get even more out of the business opportunities during the week. One of these is 'Meet the buyers' where firms can book up four meetings (for free) with large aerospace companies to 'bypass the gatekeeper' and speak straight to the decision maker. Small firms can ask the organisers to see a list of buyers and their interests in advance of the show, and then arrange for a private meeting so they can pitch more effectively.
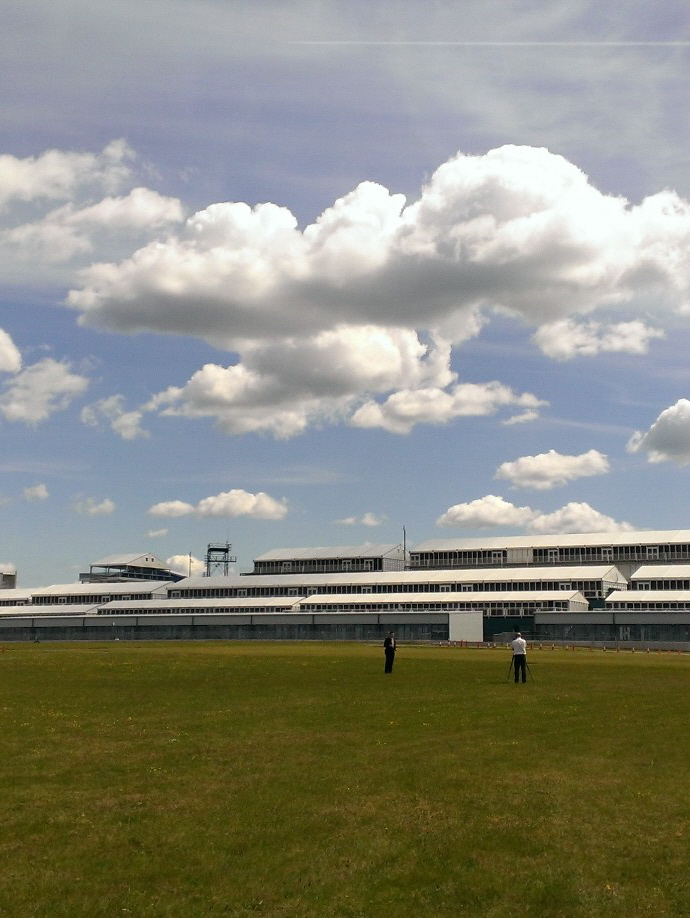
Shot of the exhibition halls at Farnborough Airport, taken in May 2014.
The Meet the Buyer programme takes place on the mornings of Tuesday, 15 and Wednesday, 16 July in Hall 1A. If firms don't want to take part in that, then access to the SME networking lounge is open during the whole week in Hall 3. The objective of the SME networking lounge is to give smaller exhibitors an opportunity to network in a dedicated area. It's furnished as a lounge style environment with café facilities and exhibitors can host clients and potential business partners in a dedicated area away from their stand.
There's also a three-hour long Supply Chain Conference (SC21) on Thursday, 17 July that will be well worth attending, as well as other commercial manufacturing briefings to find out more about the capabilities required to become a partner in an OEM supply chain. The biggest opportunity this year might be the Commercial and Civil Delegations programme, which was tried out for the first time in 2012. It returns this year and allows firms to have personal introductions to individuals not generally accessible to the open market. The programme gives access to representatives from commercial organisations such as OE/Tier 1 manufacturers that are involved in current new aircraft/rotary development programmes that present opportunities for the supply chain. Even better is that there is no charge.
There might still be self-build stand space available, but at the time of writing 98% of this had been sold. The UKTI Tradeshow Access Program (TAP) program has 30 grants of £ 1,500 to go towards the cost of a stand, but these are being snapped up and at the time of writing only two remain. The organisers are asking the UKTI to see if they can get more (basic stand space in a hall starts at around £ 5,000 for the week).
Summing up his thoughts on this year's Farnborough, Mr Ormrod says the show will represent three things; the return of the growth of the economy, the largest international audience they've ever seen and the largest group of SMEs that will be attending any aerospace exhibition on the calendar.
If you hadn't heard, the F-35 jet is going to be flying at the show for the first time. A sight, no doubt, that hundreds of firms in the UK will be proud to see and due reward for all their work in developing and making parts for it. Wing Commander Jim Schofield has been the UK's test pilot on the jet, and said at the media day that it's a mature programme, and that (surprisingly) one hundred of the jets have already been manufactured. Britain has contributed £ 1.2 billion towards its development and will spend even more when it buys 14 of them. Stealth is a key aspect in the F-35's design, yet the shapes of the surfaces you see on it, and on many of today's modern aircraft, are only possible thanks to advances in CADCAM.
Needless to say then that big software firms like Open Mind, Delcam and CGTech are exhibiting during the trade week. Open Mind Technologies (01869 290003) will be on Stand B3 in Hall 1 to give the UK aerospace industry its first look at hyperMILL 2014 and managing director Adrian Smith says he's going because he wants aerospace manufacturers to witness what has been achieved in the marketplace with hyperMILL to date.
Delcam (0121 683 1000) will be on a pod within the Midlands Aerospace Alliance stand (B14 in Hall 1) and will talk about both PowerMILL and what its Professional Services branch can offer. Delcam's marketing manager Peter Dickin says PowerMILL has been used, at some stage, on virtually every major aircraft programme in recent years. A recent development with PowerMILL is the ability to use it to program a Hermle C60 5-axis machining centre to cut fir tree profiles rather than having to use specialist broaching equipment. The new offering from Delcam's Professional Services is in the programming of a new hybrid machine from Hamuel Maschinenbau (01386 793 443) for the remanufacturing of turbine blades. The hybrid machine offers 5-axis CNC milling, laser cladding, robot polishing and laser marking all in one unit, so it costs a fraction of the price of a multi-machine repair cell, as well as saving on floor space. The machine mills off the damaged material on a turbine blade and then builds the material back up using laser cladding. Five-axis milling then creates a smooth transition between the original part and the new material. The blade is then polished and laser marked on the same machine, if it's needed. Where Delcam fits in to this is in providing the adaptive machining software that is used to work out how to orientate the parts, to assess defects and to ensure each process is undertaken accurately.
CGTech (01273 773538) will be on stand D10 in Hall 1 showing version 7.3 of its Vericut software. Aerospace firms might also be excited by CGTech's new Composites Applications software. This can be used for programming and simulating of Automated Fibre Placement (AFP) and Automated Tape Laying (ATL). CGTech will show examples of what can be achieved. These include a large one-piece fuselage barrel on an Electroimpact multi-machine AFP fabrication cell; a U-channel structure on a 7-axis mTorres AFP machine; and several examples using AFP heads mounted on 6-axis robots from KUKA, FANUC and others.
Renishaw will be on stand FT2 in Hall 4 and says it has been developing products specifically for applications in the aerospace industry, adding: "We are confident that there is not a plane in the sky that is not in some way touched by processes or components that use our metrology products."
The entire Renishaw range of metrology products is used within the aerospace sector, from probes for machine tools and CMMs, through to calibration and gauging systems, as well as its laser-based position feedback encoders, will be promoted. The firm says: "Our linear encoders are also used to aid positioning on machines used to assemble wings for a range of Airbus planes including the A320 and A380."
Renishaw also has metrology systems that can be used to help manufacture turbine blades. One of these, Sprint, is a high speed contact scanning system for machine tools that aids blade tip refurbishment and root blending. Sprint is used in conjunction with the firm's Revo, which is a 5-axis scanning system for co-ordinate measuring machines (CMMs). Most impressive is Renishaw's Modus aerofoil analysis software for the calculation and reporting of blade section profiles and its SurfitBlade software to aid reverse engineering of the complete aerofoil.
Renishaw will also be showing off the huge benefits of its metal additive manufacturing (AM) machines. Head of communications Chris Pockett says: "We are now working closely with many leading aerospace companies to help them adopt AM processes to produce complex, lightweight, fully dense metal components. In the highly regulated aerospace industry, innovative new manufacturing techniques can take time to become accepted as standard practice and approved processes, but the potential benefits to the aerospace sector are huge and we aim to be at the heart of this change."
Mitsubishi Materials UK (01827 312312) returns to the show and reports it is becoming steadily more involved in the aerospace sector in the UK, through the supply of high performance cutting tools. It says there are several Tier 1 and Tier 2 aerospace suppliers currently using Mitsubishi products in aluminium wing spar milling and on several brake and landing gear components that require high volumes of titanium machining. It is also involved with benchmark testing of new components that require extremely deep pocketing and profiling of titanium alloys. A further project is looking at many new machines that will be milling wing spars where MQL machining (Minimum Quantity Lubricant) will be a key factor in how efficiently the new machines can be utilised. Two of the newest breakthroughs in cutting tools will be on the firm's stand at Farnborough, namely the VFX5 milling cutter and the iMX endmill that uses exchangeable heads. The VFX5 is a smaller version of the successful VFX6 series and are available in diameters 40 mm to 80 mm in coarse and fine pitch types. The cutters can take smaller XNMU16 size inserts with corner radii in sizes 0.8 mm to 5.0 mm. Metal removal rates of up to 500 cm³/min have been achieved while also maintaining acceptable tool life.
The iMX end-mill is for titanium alloys and heat resistant alloys (such as Inconel) and users can chose from 12 different geometries of head in diameters from 10 mm to 25 mm.
Mitsubishi Materials UK says it has just signed up to the SC21 programme (Supply Chain for the 21stCentury) which is now a well-established accredited improvement programme, overseen, governed and managed by ADS on behalf of UK industry. The firm expects to receive its official accreditation of SC21 at the show.
While Mitsubishi Materials UK is involved in milling wing spars, Marposs (024 7688 4960) says the airframe manufacturing process is becoming more automated and so is the requirement for traceability and the ability to audit the process. As such, Marposs says it is expecting to see an increasing demand for its measurement and machine tool monitoring products. Marposs has also recently acquired an aerospace tooling company based close to Paris - Kern Industrie - well known and well respected for producing specialised equipment for the repair and maintenance of aircraft engines. "We are mainly in the civil sector as our products are ideally suited to the high volume, high precision environment," says UK sales manager John Beaumont. "We can't say exactly what work we are doing, but it is fair to say that Marposs is working with most major airframe and engine manufacturers worldwide."
Starrag Group (0121 359 3637) will show off its expertise in the production of primary structural components for fuselage, tail unit and wing areas, as well as its machining of turbine blades, blisks, casings and fuel system parts. It also makes gyroscope components, electrical connections, sensor parts and gear components. Visitors to the firm's stand (in the Swissmem area), will be able to gain details of all Starrag solutions, including Droop + Rein machines for landing gear applications, Berthiez for engine casing boring/grinding, Starrag 5-axis blade machining centres, as well as Ecospeed high-speed machining centres which, on aluminium workpieces, can achieve floor-to-floor time savings of 60 per cent by transforming a four-tonne billet into a 120 kg complex structural part in less than 20 hours.
Other firms at the show
Breton
Donaldson Company, Inc
EOS – Electro Optical Systems
Leistritz Turbinentechnik GmbH
FIVES
Geometric Limited
Grob machine Tools UK Ltd
Mitutoyo (UK) Ltd
Oerlikon Balzers Coating UK Ltd
OSG UK Ltd
Schuler Pressen GmbH