Contents and links:
- Introduction
- Fierce competition at the entry level
- Supplier investment is a sign of the times
- IPG: The largest in the world
Although only 50 years old, laser technology continues to develop at a rapid pace; one type in particular is coming to dominate sheet metal processing. Lasers using an electronic diode, similar to an LED, as the light source are winning out over an older technology that uses CO2 gas in the laser. Machine makers and laser source providers are investing to support future growth.
When lasing happens inside a fibre optic strand (that then also carries the light to the cutting head), it is called a fibre laser. When lasing happens inside a crystalline disk (connected to a fibre that carries the light), it is called a disk laser. The main proponent of this latter, longer-established alternative, laser and metal processing machine manufacturer Trumpf, argues that the disk laser is more robust than the fibre laser, because of reduced sensitivity to back-reflections at high power.
Whether fibre-generated or fibre-carried, these lasers are generally less expensive to operate than CO2 lasers for many types of metal processing, as they require not only less electric power but also none of the process gas supplies that CO2 lasers need. For example, the new dealer of Kimla profiling machines in the UK, MBA Engineering (01132 385 400), estimates that its profiling machine’s running costs using an IPG Photonics-made 4 kW fibre laser are less than half that of a competitor’s machine powered by a 4.4 kW CO2 laser (£1.78 per hour compared to £5.03, averaged over a year’s worth of 24-hour/5-day running, assuming 55% beam on time, £0.10/kW electricity cost and a quotation from gas supplier BOC).
This new partnership, which has yielded four sales since late 2015, is part of a bigger market trend. As the industry becomes more familiar with solid-state lasers, and as they become more popular, there are an increasing number of machine builders able to work with them and deal with their radiation requirements (for example, light-tight enclosures are required in the EU).
FIERCE COMPETITION AT THE ENTRY LEVEL
Competition is fiercest in standard machines without special features, according to Peter Kallage, manager of the Hamburg applications lab of German CO2 and fibre laser system manufacturer Rofin-Sinar, which in this market supplies Belgian laser profile machine manufacturer LVD, among others, and offers other types of lasers, too. He adds: “There will be tough competition in the markets in the future.”
The Amada LCG-3015 AJ fibre laser profiler features a fibre laser source co-developed with Lumentum
A new machine on the market responding to the cost driver is the LCG-3015 AJ fibre laser profiler from Amada (01562 749500). Intended for the job shop market that doesn’t require the highest levels of accuracy available with its previously-launched top-of-the-line model, the new LCG-AJ machine incorporates a fabricated – rather than cast – frame, to reduce cost.
The machine, to be launched officially at the EuroBLECH 2016 show in Hanover, also features a 6 or 9 kW laser source, both comprising the third generation of fibre laser technology developed with US laser manufacturer Lumentum, formerly known as JDSU (from which the model designation ‘AJ’ is derived; the machine’s laser source is developed by the Amada-JDSU partnership).
Gary Belfort, engineering manager for Japanese sheet metal processing brand Amada in the UK and other European countries, explains that Amada is a shareholder of Lumentum, and that their development partnership is bilateral – there are even reciprocal staff exchanges in the Amada R&D department at Fujinomiya, Japan and Lumentum’s in San Jose, California. As a result, the technology coming out of this collaboration is restricted to Amada machines, although Lumentum also sells other lasers to the global machine builder market.
Another cost-sensitive product launch at EuroBLECH is from Trumpf (01582 725335): its new TruMatic 1000 combination punch/fibre-carried laser machine, powered by a 3 kW TruDisk fibre-carried solid-state disk laser. This model is the company’s first laser-punch combination machine at an entry-level price point, which Trumpf says makes the move from 2D laser processing to laser-punch capability easier for customers.
Sheet metal profiling machines are being launched into the market that are specifically adapted to the needs and advantages of a fibre laser source. The ByStar from Bystronic (0844 848 5850), for example, unveiled in the UK at a July Open House (see also article), is said to be the company’s first built specifically as a fibre laser profiler. Its previous model, the BySprint, is fitted as standard with a CO2 laser source, although a fibre laser source is optional in the BySprint Fibre range. ByStar features include a new chassis construction; to enable higher positioning speeds, there are linear drives for bridge and carriage travel, instead of the BySprint rack and pinion drives. The machine was launched with a 6 kW IPG Photonics fibre laser source. It also features, for the first time in the Bystronic range, a Bystronic-made SSC cutting head.
As volumes ramp up, laser sources are also getting more powerful, enabling quicker cutting of sheet metal and allowing cuts of either thicker steels, or non-ferrous materials. This change is driven by technological developments among suppliers, according to Kallage from Rofin. He adds: “High powered lasers have been on the market for a long time. But the process developments in the last three, four, five years are able to handle higher laser powers, especially for fibre lasers. This means development of the process head, centring and so on. It is all about bringing power to the sheet that you want to cut.”
SUPPLIER INVESTMENT IS A SIGN OF THE TIMES
Rofin itself is being acquired by US laser manufacturer Coherent, in a $942 million deal announced in March 2016, partly to strengthen Coherent’s materials processing segment. This seems to be another sign of the times; just one of many moves over the past 12 months or so that is drawing together suppliers of industrial fibre lasers more closely with the machine builders that buy them.
For example, fibre laser manufacturer JK Lasers of Rugby was acquired by SPI Lasers (01489 779696) in April 2015 to increase its portfolio of high power fibre lasers (up to 4 kW). SPI is also a subsidiary of Trumpf, but does not supply Trumpf’s metalcutting machines; lasers for those machines, and many others (including true fibre lasers) are made in two factories in Germany.
A Trumpf TruDiode 6006 light source. Trumpf opened a diode R&D facility in Berlin last year
The Schramberg, Germany factory that makes disk lasers for Trumpf’s 2D laser profiling machines is to be expanded in a €30 million project, the firm announced only two months ago. The expansion will double production, allowing the company to prepare for what it calls double-digit growth in solid-state lasers over the next 5-10 years.
That follows the opening of a new laser diode centre in Berlin last October, close to several German state research institutes.
At the time, Dr Berthold Schmidt, head of the central department for R&D at Trumpf, called the centre of ‘crucial importance’ for development: “We’re attempting to look 10 years ahead here, and to lay the foundations for future applications.”
However, Trumpf is no longer the only machine manufacturer that also makes its own laser source. Earlier this summer, Italian sheet metal machinery manufacturer Prima Power (024 7664 5588) showed a new 3 kW fibre laser source, the CF 3000, at the company’s new Italian headquarters (see article). It is made by its Massachusetts subsidiary Convergent Photonics. At a press event marking the opening of the facility in June, Claudio Banchi, executive vice president sales for the EU, stressed the significance of manufacturing both the machine and the laser source: “This is really important in a competitive market to offer the complete package to your customers.”
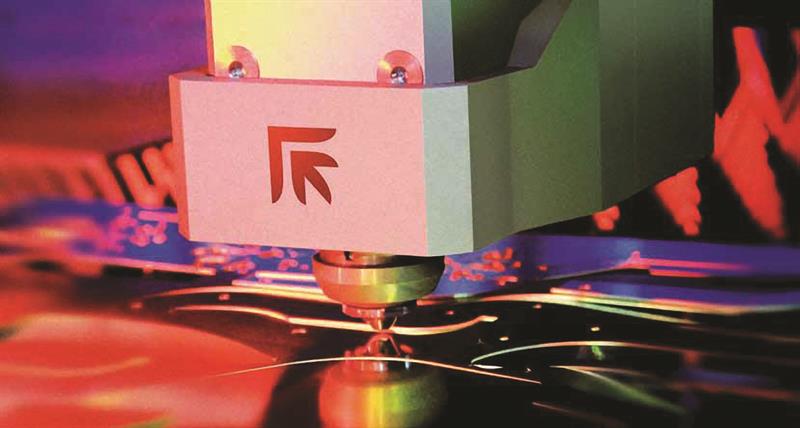
CEO Ezio Basso explained that the project began 11 years ago, but has evolved since then. A 4 kW fibre laser is under testing; a 6 kW model is forecast to be launched next year. He said: “We are convinced that if you want to be one of the major players in 2D and 3D laser machines, you need your own laser.”
This year, it expects to ship about 50 profiling machines with the Convergent laser, the bulk of its deliveries will continue to be fitted with a fibre laser from principal supplier IPG Photonics; over the next few years, it will ramp up internal production and ramp down external purchases.
In the meantime, Prima continues to buy the diode, from Lumentum, but has begun an R&D project with the (local) Polytechnic University of Turin that aims to allow it to assemble diodes produced by a third party, and to develop its own diode production. When asked why Prima was pursuing this project, Basso said in June: “The cost of a fibre laser is 50% related to the diode. This is a point. We need to decrease the cost of our laser. To be competitive with buying the diodes from the market is very, very difficult.”
The largest fibre laser manufacturer worldwide is IPG Photonics (0117 203 4060). According to its 2015 annual report, IPG shipped in total 32,800 lasers in 2015; it estimates about half of those were used for cutting, welding and brazing applications.
Mark Thompson, its UK director of sales and service, holds up the company’s product reliability and vertically integrated manufacturing structure as a unique commercial advantage: IPG manufactures all of the elements, including fibres and diodes, in-house. He says: “That allows IPG to quickly respond to market trends for a wide range of fibre laser products.” UK sheet metal profiling brands that use IPG sources include Kimla and Prima of course, as well as Bystronic, Yamazaki Mazak (01905 755755) and others.
And IPG’s product range continues to expand. First, IPG has started making process heads, another key component in a profiling machine that directs the laser beam on to the material being cut. Faced by a market shortage of heads for lasers above 4 kW some years ago, IPG Photonics started to design and manufacture cutting heads; it also offers heads for welding and galvo scanning applications, Thompson reveals.
In another development, IPG launched the LaserCube machine at the MACH 2016 exhibition at Birmingham’s NEC in April. It is a small-format (1,219 by 1,219 mm), automated flatbed cutter that serves a niche market for job shops. Explains Thompson: “Generally, the major integrators offer cutting machines with large cutting beds: 8 by 6 m for large industrial sheet metal and carbody parts. The LaserCube better serves those producing bespoke and smaller specific industrial products, with a high level CAD automation package.”
As the popularity of its products grows, IPG has expanded its footprint in the UK with a 5,000 ft² sales and service centre near the Bristol aerospace hub. Thompson estimates that UK manufacturers consume over 100 high power (multi-kW) laser sources a year; and it is this growing machine tool installed base that his team is tasked to support, as well as supplying lasers for other applications. IPG Photonics continues to invest in the UK, with plans to further expand the number of permanent UK-based field service engineers.
A car part trimmed on Prima Power’s LaserNext multi-axis laser profiler using the firm’s own fibre laser. Mark Thompson, IPG Photonics UK director of sales and service, argues that the switch to aluminium car body parts from steel has driven adoption of fibre lasers, which are technically better suited to that more reflective metal
What all of this means is that the supply chain has recognised that high powered solid-state lasers, whether fibre-generated or fibre-delivered, have defeated their CO2 technology rival. Having realised that, suppliers are now lining up to invest for the long term.
This is good news in the world of the subcontractor. For most metal processing applications, these lasers perform better than CO2 and are continuing to get better; and, partly through competitive pressures, they are becoming less expensive. Even if now might not be the right time to invest in a new unit, factory managers needn’t worry: solid-state lasers are here to stay, and are becoming ever more affordable.This article was first published in the September 2016 issue of Machinery magazine.