Wallwork director, Simeon Collins, explained: "We invested significantly in new plasma nitriding capacity last year, bringing in a Rübig Micropuls Everest. We have now also seized the opportunity to upgrade and refurbish some of our existing equipment to meet the growing demand for plasma nitriding.”
This additional £500k investment by the group, shows their confidence in future demand, especially from the aerospace sector. The Cambridge plasma nitriding centre, provides 24/7 processing and has a dedicated area for inspection of case depth, structure and other quality aspects.
Plasma nitriding is a relatively cool process compared with other heat treatments, ensuring the dimensions and characteristics of the base metal are not compromised. Vital for the stringent requirements of aerospace manufacturers. The process meets differing needs because the depth and properties of the case hardened layer can be finely controlled. Wallwork also design and make physical masking used to ensure only the specified surfaces are exposed and are hardened.
Manufacturers of wear parts such as gears, camshafts and followers, valve parts, aero-engine and airframe components, dies and injectors use plasma nitriding to improve component endurance. For makers of stainless steel parts used in harsh environments, low temperature plasma nitriding minimises loss of corrosion resistance in the metal.
As plasma nitriding does not leave chemical residues, applying hard coatings by physical vapour deposition (PVD) is more easily achieved and imparts even better wear resistance for use in high-load applications. This can all take place at the Cambridge site.
Along with Nadcap accreditation, Wallwork holds extensive aerospace approvals from company, national and international bodies. To meet customer fast turn-around needs, their in-house transport fleet provides quick and efficient nationwide pick-up and delivery.
Sixth Plasma Nitrider to go live in November at Wallwork Cambridge
1 min read
Expanding their plasma nitriding facilities, Wallwork are nearing the completion of a programme of increasing capacity with a sixth unit. This is due to go live in November and will process components up to two metres in length. Ideal for larger aerospace parts and more.
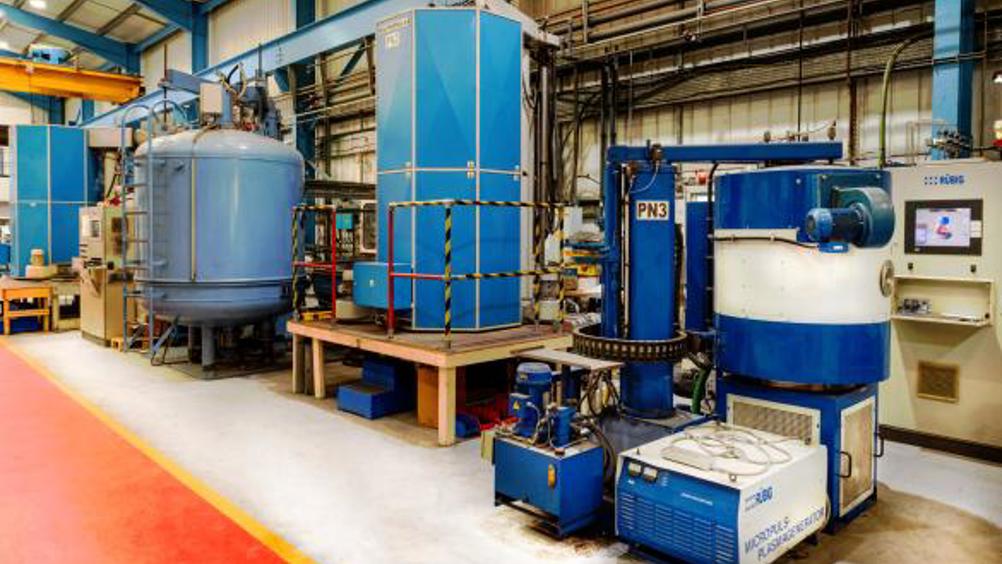