(Video shows TTOG type machine, see article for details)
Cranfield Precision has an ultra-precision machining history dating back to the late 1960s, when its antecedent was set up within Cranfield university as part of the Wilson government's 'white heat of technology' strategy (Here).
Subsequently spun out from Cranfield, it is today part of the French engineering company Fives (www.fivesgroup.com), but is a division of Fives group company and specialist cam and crankshaft manufacturer Cinetic Landis, based in Keighley, West Yorkshire (see www.machinery.co.uk/48754).
From 1980, Cranfield Precision was, and remains today, a supplier of strategic CNC technology to Cinetic Landis (Landis Lund as it was in 1980).
Forty-eight-man Cranfield Precision, based in Kempston a few miles north-east of Cranfield, Bedfordshire, has a low profile generally, but develops and delivers the highest of technology in the areas of diamond turning and optics grinding, together with related CNC equipment. Indeed, in these niche areas, it has global good standing.
With much of its work undertaken away from the public gaze, due to commercial confidentiality and such considerations, it now has two developments that will be offered more broadly – one for diamond roll turning (for PC light diffusing, distributing and brightness enhancement films, for example) and the other a new machine structure/axis configuration for grinding, turning, milling, pre-polishing and more of metal and optic parts.
Today's LCD TVs, laptop screen, tablet computers and smartphones all feature a technology that Cranfield Precision's diamond roll turning technology is aimed at producing – light diffusing, distributing and brightness enhancement films. These see light entering along an edge of the display and guided up and being 'bounced out' by a faceted surface, maximising the use of source light and, hence, supporting longer battery life. The surface geometry also influences viewing angle, important for LCD TVs, more so than energy usage.
A more mundane use of such films is in highly reflective road traffic signs, but, explains Cranfield Precision division manager Mark Stocker, they still demand highest precision film, which means highest precision machines to produce the copper-skinned rolls that are used in film production. And the levels of precision of the company's machines are staggering – the highest of all the companies in the market, Mr Stocker claims. The difference is of that between high end displays and the also-rans. The eye can see patterns very easily, he says, and the surface geometry of these rolls must comprise elements that are smaller than a screen pixel. With ever-increasing pixel densities, the challenge is clear.
BORN OF EXPERIENCE
Already being made for more than two years, with a third on the shopfloor at Machinery's visit, the EcoR1664 diamond roll turning lathe draws on Cranfield Precision's approaching 50 years' experience and technology. That means machine structure design supported by FEA, machine assembly skills, hydrostatic bearing design and manufacture, linear motor application, precision measurement, machine temperature control, vibration isolation, cutting process parameter knowledge and CNC and simulation software development.
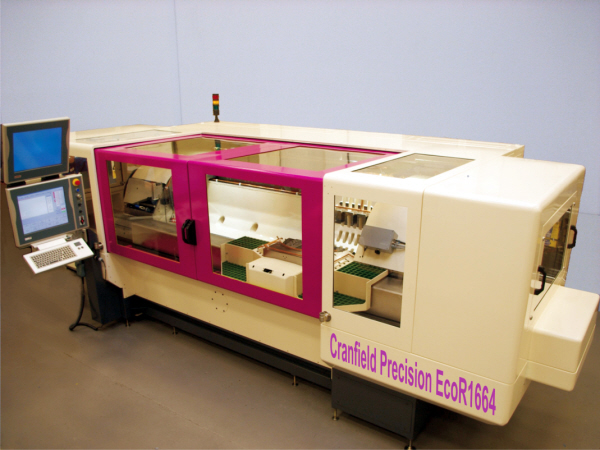
The EcoR1664 diamond roll turning lathe draws on Cranfield Precision's approaching 50 years' experience and technology
Basic capacities for the EcoR1664 are a load capacity of 410 mm diameter, 1,625 mm centre distance and 680 kg, with controllable nanometre-level precision at the tool tip a requirement. The machine has linear motors for X and Z travel, and a rotary motor for the tool's B-axis, which sits on the X-axis carriage – the tool can, but does not always, rotate about the B-axis in support of fly cutting. So, linear Z-axis, in-out X-axis, plus rotary B-axis movements, in varying relationships, generate a surface on the roll as it rotates at up to 1,200 rpm under C-axis control.
Hydrostatic technology is used in all axes and also for both the spindle and the tailstock, with oil temperature controlled to within 0.01 °C. In addition, bearing oil is controlled to 0.01 °C, while laminar flow cascade coolant, temperature-controlled to 0.01 °C, bathes machine surfaces during roll production – as long as 40 hours for course resolution; longer for fine resolution parts. "We have more temperature control experience with this kind of machine than anyone else," offers Mr Stocker.
The machine rests on air-type vibration isolation feet (<2.5 Hz), tuned to whichever environment the machine goes to, while cables pass over the machine envelope, positioned using a separate axis that is completely isolated from the main machine – in-machine drag chain use would make nanometre-level precision achievement impossible, advises Mr Stocker, although others do take that approach, he points out.
The avoidance of noise/vibration even stretches to the elimination of seals on encoders, a difficult trick when such items are being bathed in oil. And it also includes no use of bellows to cover slideways, too. There is not a single contacting surface on the machine, in fact. And the oil used in the machine also needs to be 'quiet', so pump vibration, which travels through oil, must also be isolated.
A key design attribute is that the Z-axis slideways are set at different heights (higher for the rear than the front of the machine), which means that any roll-induced error motion (rotation about the direction of the axis travel) at the tool tip is virtually zero, while bed stiffness is 1.6x greater than a conventional flat bed design would offer. As a matter of interest, it takes about seven weeks to scrape the two milled cast iron location surfaces onto which the two ground Z-axis guides are then located. Guide straightness of 5 microns or better is the aim. And even linear encoder location surfaces are scraped to match Z -axis surfaces to maintain constant read-head distance. Machines take about one year from order, with these assembled in a workshop controlled to 0.5 °C.
This results in a machine that demonstrates feed hold of better than 10 nm. "That means switching on all the drives, with any relative movement between part and tool better than that figure. If it isn't, it means there's servo buzz and that will show up as a texture on the cut groove. Indeed, if someone disturbed the environment next to the machine, with the doors open, you would see a lot more than 10 nm movement," underscores Mr Stocker.
Further demonstration of its capability is a following error (programmed versus real position) for the 750 kg carriage of 20 nm at 50 mm/second maximum traverse – a normal machine tool would be "lucky to see 1 micron". Further, because the rolls take 40 hours and more to machine, Mr Stocker adds this: "We need to know – because there could be multiple cuts, or a user needs to align the tool to a cut performed the previous day – that the tool goes back to where it was originally to within ¼ micron (250 nm). That is the really, really clever bit; the hard bit." And, finally, during a test run, the machine must be live for 40 hours, but not cutting, and the tool must not move axially by more than 200 nm and radially by more than 100 nm, proving thermal stability. "That is really, really difficult."
AS GOOD AS IT LOOKS
With all that technology, the first and key test of a good roll surface texture is visual. "You can see, just by looking at it, if there's a problem with the servo anywhere along the length," explains Mr Stocker. "We know that if we can hit these numbers [as above], we know we will get a good surface but, at the end of it, it's what does the image look like on the computer screen, for example, and people can look at the roll and know if it will produce good product."
Moving to a new machine concept, this is currently being used as the basis for an optics grinding machine for India's Instruments Research and Development Establishment (IRDE), Dehra Dun, Uttarakhand, part of the country's Defence Research and Development Organisation. The first has been delivered (TTOG-400; 400 mm diameter capacity); the second, TTOG-100 (100 mm diameter), was on the shopfloor as at Machinery's visit.
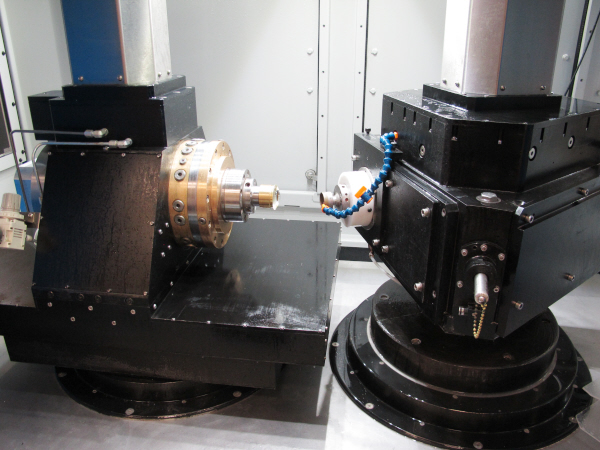
The TTOG-100 machine has a unique construction and properties - production of such machines in various sizes and configurations is anticipated to be at the rate of 30 per year
The concept, which is patented, sees a machine with two vertical rotary axes at fixed centre distances, with one linear axis mounted on one of the rotary axes. Grinding spindles, or other tools, are mounted on the linear axis. The rotary and linear axes can be hydrostatic or aerostatic, depending on load, while both chuckers and between-centres styles can be delivered. Three-dimensional freeform grinding is supported.
Originated at Cranfield Precision, the prompt for its development came from Cinetic Landis, which wanted an extension to its core machine business via a novel machine capable of high precision machining of difficult materials for parts in the aerospace and medical fields, for example, although it was also to combat loss of sales for Cinetic Landis' angle-head grinders, used in crankshaft grinding lines, by coming up with a lower cost machine design, explains Cinetic Landis managing director Roger Coverdale.
Explains Mr Stocker: "Roger asked us for a platform that he could put different things on; for a machine with reduced set-up time – this machine only has two axes that need to be aligned, relative to each other, everything else you measure and correct; and a machine that is versatile, so we just came up with this.
"Effectively, what we did, we had a sketch of a component and sketch of a wheel, and we asked 'how many different ways can you move that wheel relative to the part, what axis configurations do you need?' One of the requirements was it needed to be easy to load the part, so why not use a rotary axis to bring the part to the front of the machine. And if you can use that axis to load the part, can you use it for machining. Okay, let's try two rotary axes and see what happens; what do you need to grind a cylinder, for example? Well, you need a linear axis to compensate for the distance changes as you move around the angle. Once you do that, you say 'well, we only need three axes to do everything'."
Mr Stocker explains: "This layout, with fixed centre distances, has many advantages. One of those is that the maths required to calculate the motions to machine any shape is relatively simple, and you can machine any shape. Also, straightness error correction for the linear axis need only be undertaken once, regardless of what diameter you are grinding. With moving centres, that wouldn't be the case; you'd need a complete error map of the full 2D working area. And the only alignment required in build is for the two rotary axes – they must be square and perpendicular to each other. From then on everything else is measure and correct.
"More, if you program it properly, you can maintain tool surface-normal all of the time. That means you can choose a point on a grinding wheel to be in contact with the part and it will be in contact all the time. That has a huge benefit, in terms of surface quality, as the wheel tends to take the shape of the optic you're machining, which means you get a very consistent surface and that means you don't have to polish one area more than another.
"And there is also a benefit coping with grinding wheel out-of-balance forces. If the wheel is positioned to cut so that force passes through the centre of the rotary turret, the force is not being resisted by a servo but by the stiffness of the axis. But, even if there is an effect, it is only a second order error, as the wheel wipes past the optic and doesn't crash into it.
"Further, with fixed centre distances, it is easy to keep process coolant away from the base of the machine. On a conventional linear axis machine tool, you can't prevent coolant from getting on the machine base. So, the base is moving, due to thermal changes. Ours never sees process coolant, so is thermally stable," states Mr Stocker.
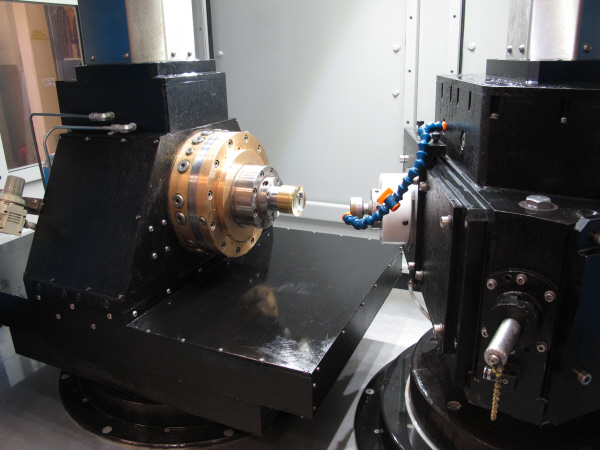
Grinding optics on the new machine
The machine's construction also makes for a very stiff, thermally stable unit. In terms of stiffness, hydrodynamic rotary axes have radial and axial stiffness of 10,000 N/ micron, while the two rotary axes are bolted either side of a granite slab (lapped to a couple of microns), so any tendency for the centres to be pushed apart is similarly tiny, while granite is also thermally stable – this granite slab arrangement is part of the patent. And this inherent thermal stability also means that cooling of the hydrostatic oil need only be to 0.1 °C – "an order of magnitude cheaper than controlling to 0.01 °C," he underlines.
And the proof of this? Optics ground, without correction (following feedback of measurement data from a Form Talysurf), where peak to valley form error (with surface texture filtered out) is better than 0.6 micron. "It takes 30 mins to machine that 65 mm asphere, which means this demonstrates both dimensional and thermal stability. And we can do better than that, if you do a correction run. On an alternative machine, that 0.6 figure would be a few microns – 2 or 3 would be pretty good without correction."
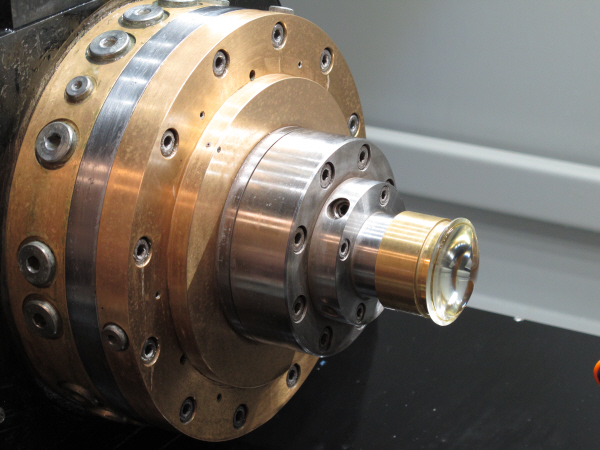
A rough finish that is too good to be true?The India customer thought so
Indeed, the grind quality achieved on the TTOG-400 was such that its Indian customer was sceptical that it had not been polished. The optic offered a clear view through it, whereas other rough machined parts would be cloudy – meaning sub-surface damage. "That means that all the effort put into producing low form error you start to lose, as you have to take 20-30 micron off to remove the damage when you start polishing. Then you have to start correcting. Off our machine, they can start to correct straight away. And with surface damage, polishing is required before you can measure for correction, using a conventional interferometer – a special infrared interferometer is needed otherwise. With our machine, you can measure straight away using an interferometer compatible with polished surfaces." Finished polishing after grinding takes surface roughness down, routinely, to 2 nm Ra, in some cases to 0.5 nm Ra, using technology from UK company Zeeko (01530 815832), with which Cranfield partners.
PRODUCTION CAPABILITY FIRST
The TTOG machines deliver, for the first time, production environment optics machining, as opposed to an R&D type machine and environment, which is what Cranfield Precision's 1990 Nanocentre machine (three of which have been made) supported at much higher cost and at much lower production rates. And form accuracy for the production machine is very close to the Nanocentre's capability at much lower cost, highlights Mr Stocker.
But the new patented common machine platform offers a new general solution for high accuracy, difficult-to-machine parts, including turbocharger, fuel injection and medical parts. And Cinetic Landis will focus its application efforts there, with all base units being built at its Keighley, West Yorkshire factory. "We're looking at 30 machines/year," offers Mr Coverdale.
First published in Machinery, April 2014